Change is Needed Today for a Future Net Zero World
Significant changes in all industrial operations are required in order to meet the World Net Zero Emissions goal by 2050 while continuing to deliver the necessary energy and goods to sustain the global economy.
However, instead of waiting for improvements and technological advances over the years or decades, existing continuous processes can be optimized to reduce carbon footprint today. Imubit’s AI has helped refineries and petrochemical producers optimize their plants by directly controlling key parameters, resulting in a new level of sustainable operations. Producers have improved their ESG performance using Imubit’s solution by increasing yields, reducing energy consumption, controlling environmental constraints, and optimizing renewable processes.
Yield Improvement &
Waste Reduction
On average, a yield improvement of 1-3% can result in annual bottom-line value worth tens of millions of dollars. Furthermore, meeting product demand through inefficient plant operations leads to increased feed rate requirements, additional waste products, and 1-5% additional greenhouse gas (GHG) emissions.

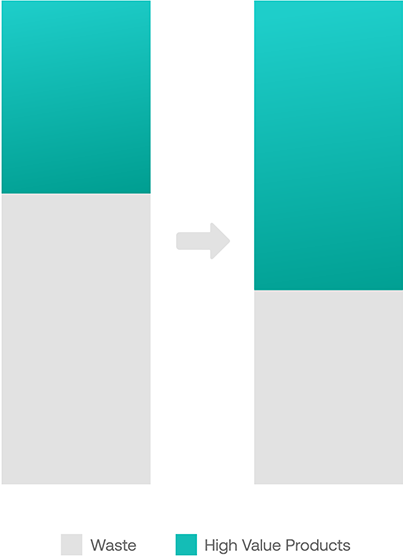
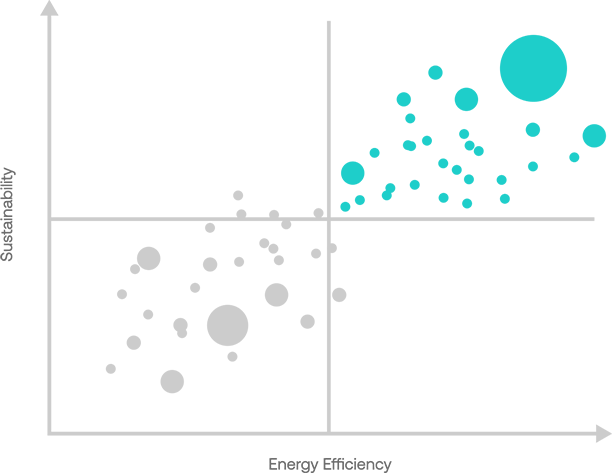
Energy Efficiency
Energy prices have risen dramatically in areas like Europe, where natural gas has more than quadrupled over the past three years and is expected to continue rising in the coming years. In addition to these increasing costs, legislation aimed at reducing greenhouse gas emissions will lead to a decrease in global liquid demand. According to a study by McKinsey, global liquid demand is projected to fall by 9% by 2025 under the 1.5°C Pathway scenario, which will allow only the most sustainable and profitable producers to survive.
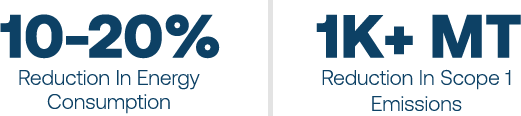
Closed Loop Neural Networks are trained to minimize energy consumption and greenhouse gas emissions while meeting quality standards. They directly control critical parameters to find the optimal sustainable solution for the plant. Adapting to changes in feed composition, fouling, catalyst activity, and even weather, these models find new ways to optimize the plant for maximum energy efficiency. Customers have reported a reduction of 10-20% in energy consumption and hundreds to thousands of metric tons of annual CO2 reduction in Scope 1 emissions.
Respecting Environmental Limits
Minimizing the release of pollutants is essential for maintaining the healthy lives of populations living near facilities. However, managing environmental limits over time is often a manual process that is not performed on a continuous basis. Furthermore, control of environmental limits can be challenging due to the interdependency of the plant and the nonlinearity of plant process relationships. These limits are particularly difficult to respect during transient states, which occur frequently in refineries and petrochemical plants. As a result, plants often violate environmental constraints or operate conservatively to avoid violation, leading to other inefficiencies.
Imubit’s models are trained to respect critical environmental limits in real-time while maximizing profit margins. These constraints can be adjusted or calculated over a longer duration to maximize plant efficiency while minimizing environmental deviations.In addition, the models are dynamic, making predicting and reducing key emissions variables much more accurate resulting in lower environmental impact and safer control.
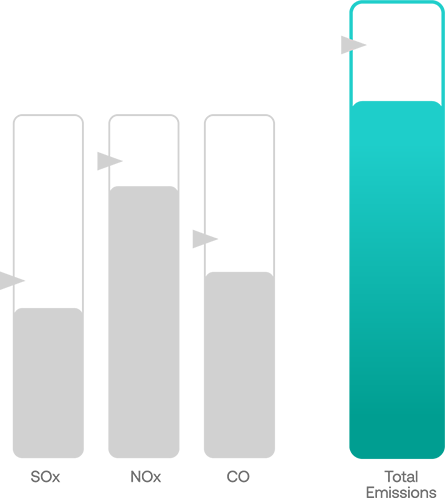
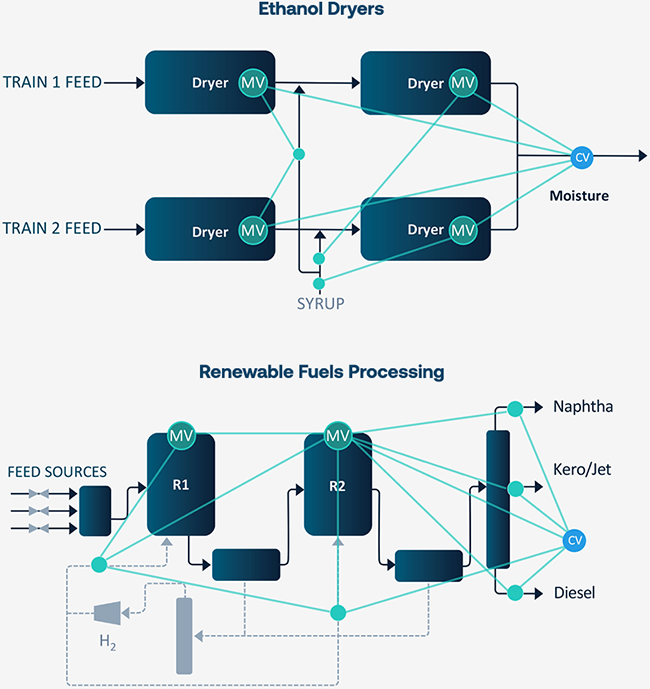
Optimizing Renewable Processes
The transition to renewable energy is crucial in achieving the global net-zero emissions goal by 2050. However, renewable energy operations present new complexities such as intermittency and variable energy supply, as well as more intricate energy grids with distributed energy sources. Additionally, sources like solar and wind are more dependent on natural conditions than human control, as supply and demand forecasting relies heavily on weather patterns and ambient conditions.
AI like Closed Loop Neural Networks offer huge advantages as they learn to manage ever-changing conditions and complex solution spaces to drive profitability of renewable energy operations. The models account for changes in composition and ambient conditions to adjust key handles within the plant to maximize operational efficiency and profitability. Closed Loop Neural Networks have been developed and can be applied to any continuous renewable processes such as ethanol and renewable fuels.