The Problem & Deep Learning Process Control® (DLPC) Scope
A client running a 115 kbd hydrocracker identified the opportunity to capture untapped value beyond existing Advanced Process Control (APC) through optimal yield management. Prior to DLPC, APC maximized feed and optimized backend fractionation, but Weighted Average Bed Temperature (WABT) targets were manually adjusted through changes to APC limits based on weekly runs of the economic Linear Program (LP) model. However, the changes were only performed on a daily, if
not weekly, basis, leaving significant value on the table. Imubit’s DLPC manipulates 1st and 2nd stage WABTs to optimize product yields while respecting key process constraints to maximize the objective function. The DLPC is integrated with the existing APC to manage lower-level constraints.
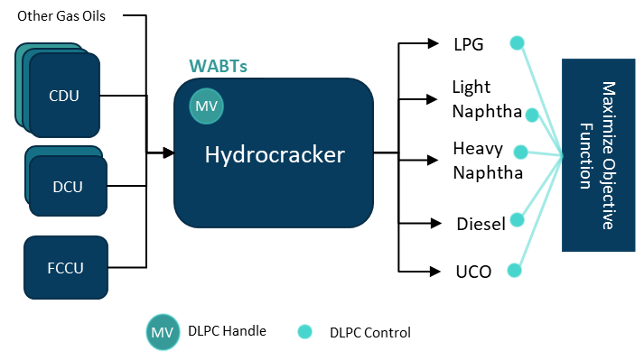
FIGURE 1 Client’s system configuration around FCCU and Crude with DLPC Design.
Value Generation
With DLPC running in closed loop, a total annualized value of $8-12 MM (at 80% engagement) was captured over two months, in comparison to a baseline period with similar operational constraints. With new WABT targets calculated dynamically, DLPC was able to increase volume swell by 0.6% which translated to an increase in incentive by almost $1.5/BBL, on top of the existing APC. The yield shift illustrates DLPC’s ability to understand the dynamics of the hydrocracker and create the most optimal yields based on prices defined in the objective function.

FIGURE 2 DLPC shift in product yields with
respect to client baseline APC data.
FIGURE 3 Increase in conversion % with respect
to client baseline APC data..
Realtime Performance
Prior to DLPC, the client’s APC relied on operators to manually adjust WABT targets based on operating orders as defined per the weekly LP run. While APC managed backend fractionation, it could not optimize the yield output from the reactors. Once DLPC is engaged, the WABT targets are consistently adjusted to capture the optimal yield from the dynamic feed composition and therefore maximizing the objective function. The objective function in this window of time increased by $20k/day.
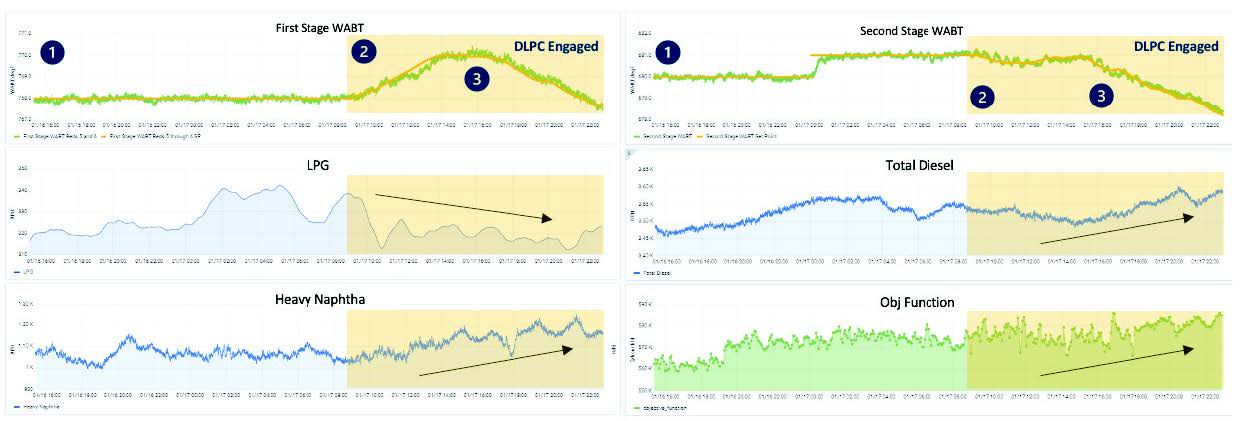
FIGURE 4 (1) Before DLPC is engaged, WABT targets are infrequently adjusted. (2) Once DLPC is engaged, WABT targets are consistently adjusting to increase product yield and maximize the objective function. (3) DLPC is responding to disturbances in the process, while still maximizing the objective function.
Resources & Timeline
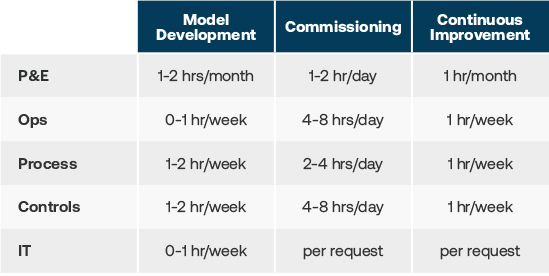
FIGURE 1 Client’s system configuration around FCCU and Crude with DLPC Design.