By Greg White, Business Consulting Engineer, Imubit
As a former Advanced Process Control (APC) Engineer, I spent many months building DMC+ models from scratch. Several steps were required, but the main ones were step testing, model simulation, and model development. Model simulation and model development were wholly contained within the APC group, but step testing necessitated operator participation and often led to frustration from both groups.
Step testing is how APC engineers acquire the data needed to represent the relationships between MVs and CVs in the process unit. It involves a very finite period of time – usually about two weeks long – where operators (at the behest of APC engineers) make set point changes in Manipulated Variables (MVs) and the APC team measures the Control Variable (CV) responses. For units where set point targets rarely change, step testing is a way to gather process data at a range of values to begin to build meaningful empirical relationships.
Anyone who has worked in a refinery or other industrial processing plant will agree that two weeks of data is hardly a representative sample of how a unit will operate over the half decade of feedslate changes, yield shifts, and fouling that occurs between major turnarounds. In an ideal case, the controller is rebuilt after every unit turnaround, however, this is a rarity due to a low perceived return on investment (ROI). The large amount of resources required to rebuild a controller is hard to justify when the goal will not be drastically different – continue to maximize high-value products up to a constraint. The resource cost mentioned above is mostly your APC engineers’ time. You’ll clock some process engineering, process safety, and perhaps instrumentation or reliability engineering time because their sign-off is usually required in the Management of Change (MOC) process. These costs, however, are dwarfed by the much larger cost of moving the refinery into a sub-optimal state in the name of data collection.
You’ve seen this film before. The APC engineer approaches the console to gather CV response data for an MV move larger than typical process noise but not so large that it disturbs the unit. Negotiation between the APC Engineer and the Board Operator ensues, and each character’s underlying motivations are revealed. The Board Operator’s ideal shift is a smoothly operated unit with stable and predictable flows, temperatures, and pressures – an easy handoff to their relief. Quality targets are met, keeping management out of their hair. The last thing on the board operator’s mind is playing along with an engineer’s science experiment which may shake up this harmony.
The screenplay of this critical [to the APC engineer] conversation usually looked something like this:
APC Engineer: [enthusiastically] Good morning! Are you busy now?
Board Operator: [groaning] Good morning… I thought I told you to bring donuts if you were going to come in here.
APC Engineer: [temporarily deflated] Oh, I thought you were joking… [enthusiasm returns] Anywho, can you increase the fractionator overhead temperature by 5 degrees?
Board Operator: [annoyed] Good grief, are you trying to dry out my LCO tray again? 5 degrees? That will back out the reflux rate too much, we won’t meet our 95% specs on products, and we can burn out the LCO pump if the tray runs dry. Go back to your office, get a better plan, bring donuts, then come back.
APC Engineer: [persevering] Well, how about 3 degrees?
Operations Supervisor: [aggravated] Hey, are you distracting my Board Operator? We need to get some hot work permits signed right now. We don’t have time to heat up the column just for fun.
APC Engineer: [deflated] If I come back with donuts would you please increase the OVHD temp by 2 degrees?
Board Operator: [compromising] Only if they’re chocolate.
Lather, rinse and repeat for subsequent step changes. The data gathered in each step test is run through the model simulation, and the outcome is one singular gain relationship. It’s no wonder the relationship between operations and APC teams can be a strained one.
Closed Loop Artificial Intelligence Optimization (AIO) takes a more modern approach to closed loop process optimization, leveraging years of pre-existing historical process data in lieu of step testing. With access to good quality data (learn more about data readiness for AI), Imubit can train a model that simulates the process plant relationships and provides predictions using only historical data. This AI-driven approach doesn’t lead to one simplified gain relationship between an MV and a CV. Rather, the output is a distribution of gains, with tens of thousands of different relationships identified over time under different real and simulated MV, CV, and DV value combinations (figure 1). With this composite knowledge of relationships between plant variables, the Imubit AIO controller optimizes the performance of your process unit toward a learned strategy. It eliminates the friction between operations and APC teams, aligning motivations and driving the plant toward the highest state of constraint-respecting operational efficiency.
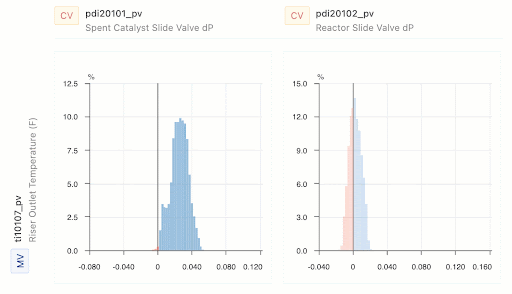
Figure 1. Imubit learns every possible relationship between two variables, as displayed in the interactive gain histograms.
Check out our new Next Generation Workforce white paper to learn how Imubit AIO technology is breaking down silos between teams and creating an empowered, technology-savvy workforce.