The Problem & Deep Learning Process ControlĀ® (DLPC) Scope
A client with a 285 kbd refinery identified an opportunity to optimize yield across two reformers, while achieving site-wide octane barrel targets on their gasoline pool during the winter season. The reformers are used as balancing octane producers, requiring frequent adjustment on feed charge and severity to compensate for swings in the overall gasoline pool. Between varying crude feed slates and the fluctuating gasoline component production rates and qualities, the client had difficulty achieving the optimal octane barrel target consistently. If the octane barrel fell below target, the client would have to sell at a discount or blend with high-value material at a loss. The reformers were also operated sub-optimally, bypassing a portion of the feed around the reformers and producing higher octane reformate with an overall loss of yield. To access the untapped value of the naphtha system, Imubitās DLPC continuously manipulates both reformer feed rates and severities to maximize liquid yields and maintain a consistent desired site-wide pool octane make, while respecting unit constraints.
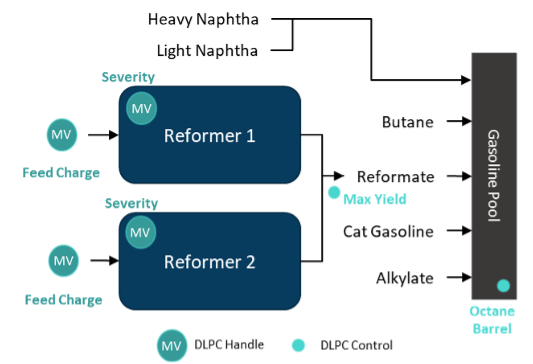
FIGURE 1 Clientās system configuration around FCCU and Crude with DLPC Design.
Value Generation
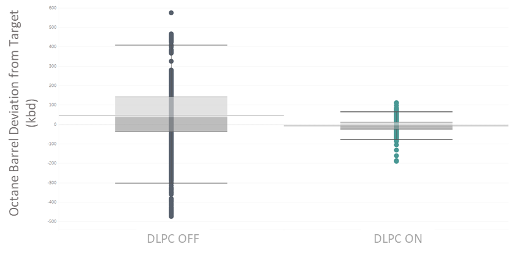
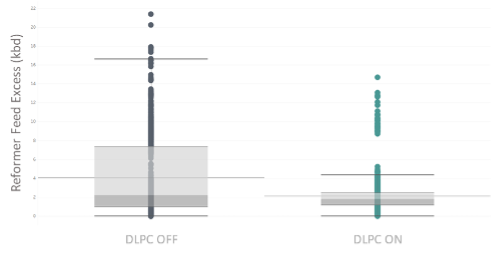
Realtime Performance
Prior to DLPC, the reformer feed charge and severity were manually adjusted using existing Advanced Process Control (APC) external targets, set by the LP and gasoline blenders weekly, to meet the overall octane barrel target for the gasoline pool. However, the reformate octane barrel produced often deviated from the overall octane barrel target, resulting in slow overcorrections and at times as the cost of reformate yield. In addition, disturbances in the gasoline pool have long-time dynamics and non-linear responses, causing large swings to the overall octane barrel production making it very difficult to optimize. When engaged, DLPC manipulates the feed charge and severity on each of the reformers to proactively control the reformate octane barrels produced to the octane barrel target while respecting critical operating limits. With the ability to predict impact and respond to disturbances dynamically, DLPC can adjust the reformers, continuously minute-by-minute, to consistently optimize the reformate octane barrel to the desired octane barrel production with operational stability.
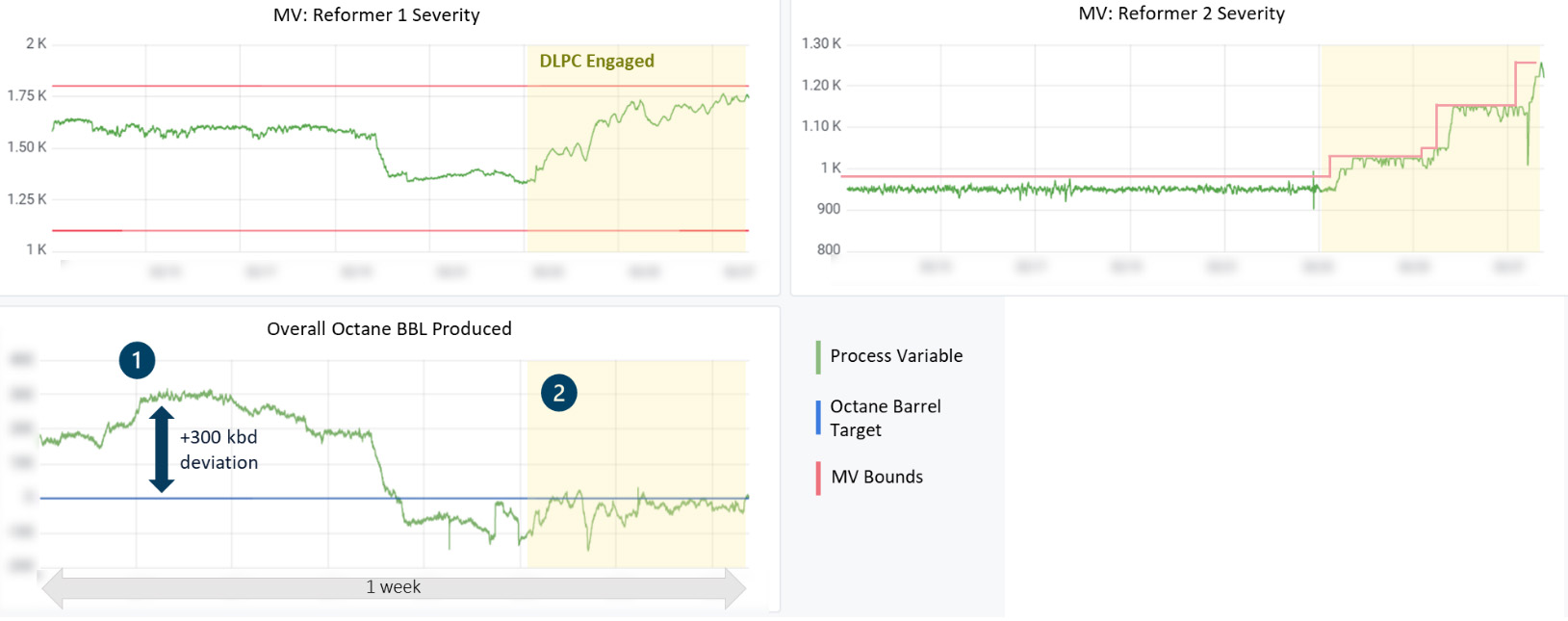
Resources & Timeline
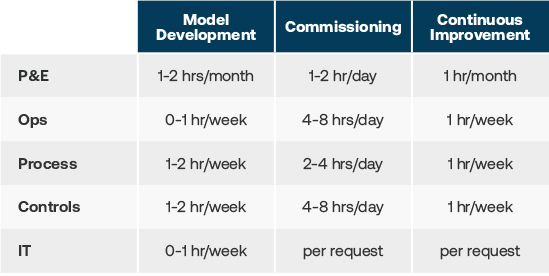